this page: http://www.bacomatic.org/~dw/sixto/sixto-0.htm
Sixto Bernal, one of the members of the Fordnatics mailing list, is building a
3.6" stroke 289 for 366 cubic inches. He ran into trouble getting it balanced
- essentially, no shop he found in his area could do it. I figured I could.
I did, but it was one of those "never again" things. Basically, Sixto's
problem was by the time he trimmed the counterweights down so the pistons
didn't slam into them at BDC, there wasn't enough counterweight to do the job.
Sixto's crank has something like eight *pounds* of heavy metal and lead in it;
the counterweights are essentially cast iron lattices filled with tungsten
alloy and weld. I wouldn't want to do another like this, but I managed not
only to balance it, but I balanced it to the stock 28oz damper and flexplate,
which I thought was a major accomplishment.
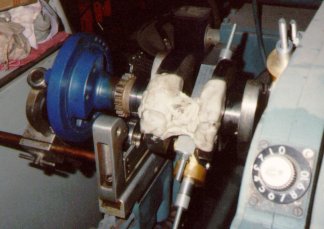
As it arrived; several pounds of clay were required to keep the crank from
hopping off the rollers. The crank had been stroked by Rigo Saltero in
California; you can't tell in this photo, but he did an excellent job.
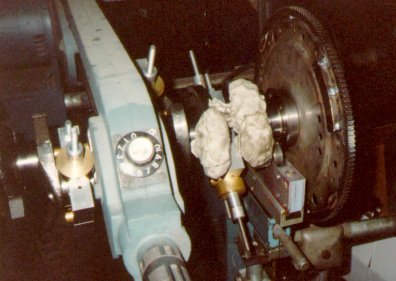
The other end; still more clay.
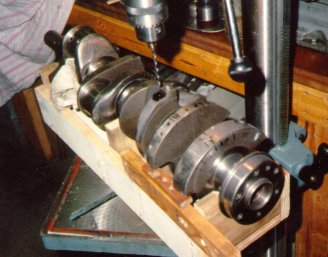
Marked places for the first batch of heavy metal, pilot drilling holes. The
crank is so far out of balance I'm installing the maximum amount of heavy
metal in each counterweight, which means inserting slugs of heavy metal
radially.
Note wooden box that holds crank so it can't bend under the
drill pressure.
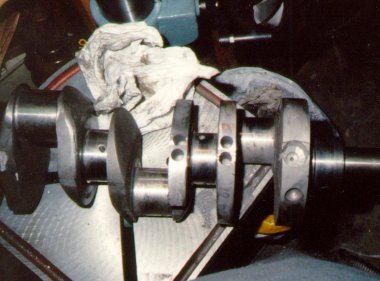
Drilling holes for the first batch of heavy metal. All the
counterweights will wind up being filled in the end, so I'm
doing them all at once. Normally you'd fill the front and rear
counterweights first, but since I'm pretty sure I'll need everything, I'm
starting with the middle. If I wound up not needing much in the ends, having
the weights inboard would reduce the load on the crankshaft. Alas, the crank
needed all except the rearmost counterweight completely filled.
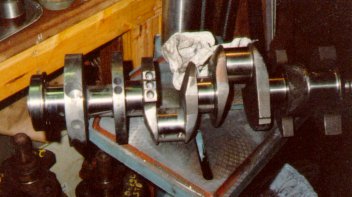
Getting ready to hammer in the heavy metal. Note "terraced"
notches so drill could start square to crank. This all gets welded up later.
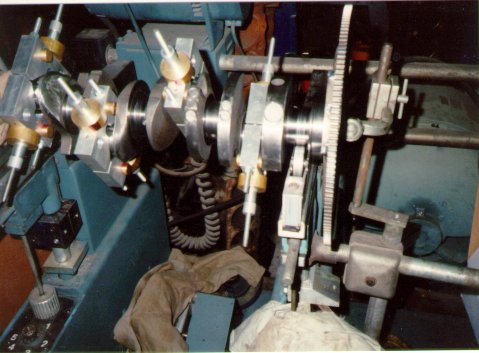
Testing, still a long way to go. The crank was probably on and off the
machine fifteen times; each time the weights have to be removed and
reinstalled in precisely the same places. It's a time-consuming job.
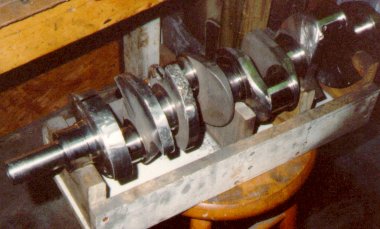
In progress; some heavy metal is welded over.
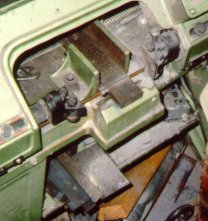
Cutting blocks of 5/8" cold rolled steel to add to middle
counterweights, to get every last bit of mass possible.
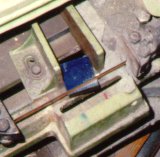
Sawing blocks off at an angle for less grinding.
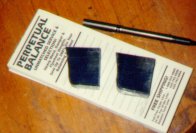
Profiled counterweight blocks, hot off the bench grinder.
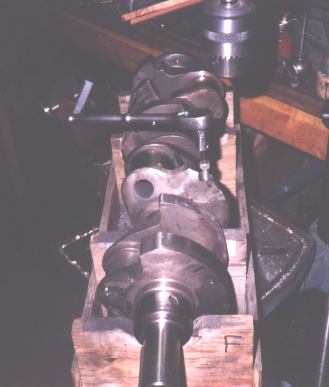
Blocks have been welded on, welds ground down, blocks ground to clear the
block and contoured to meet the rod throw, clearance hole drilled through to
the crankshaft material, the crank has been drilled and tapped, the block has
been counterbored for the bolt, and I'm running a grade 8 3/8" fine thread
bolt in to help retain the block. I don't entirely trust welding steel to
cast iron with the MIG welder; if one of the blocks were to come loose it
would be catastrophic. The bolts got tightened to 45 ft-lb. Not much chance
of anything coming loose; they're larger and stronger than the engine's 5/16"
rod bolts.
Note the front counterweight has been entirely welded over all the
heavy metal and steel plugs and the edges are squared, to get every last bit
of mass possible on the OD. There has been some grinding on the front rod
throw to take some weight off the pin side. You can see the #4 throw in the
background; notice it has some weight that could have been removed if needed.
Fortunately the back wasn't as far out of balance as the front. The SBF's
imbalance is different on each end.
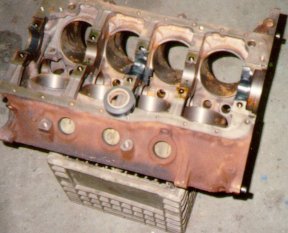
Laying some tape in an extra block - I didn't have any of
the right size main bearings handy - to see if the extra
metal welded to the crank would hit anything.
Unfortunately those are all the photos I have available. It took a set of
lightweight wristpins to make it, but it finally balanced out!
Return to Dave Williams' home page: http://www.bacomatic.org/~dw/index.htm